Sterling Ripper
Sterling Ripper literally means excellent and outstanding rock breaking equipment!
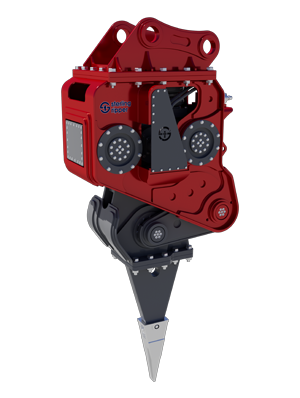
/ Job Applications
Significantly wider offering & 4 market segments enable further success!
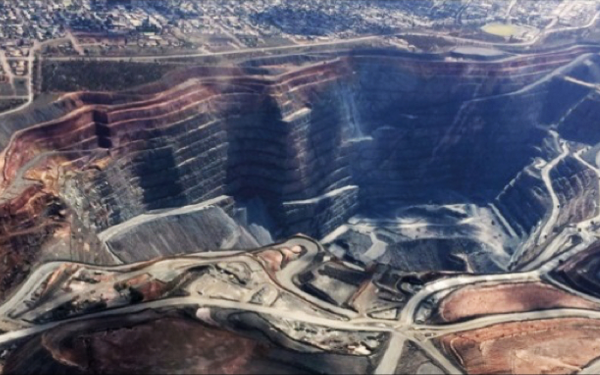
Mining
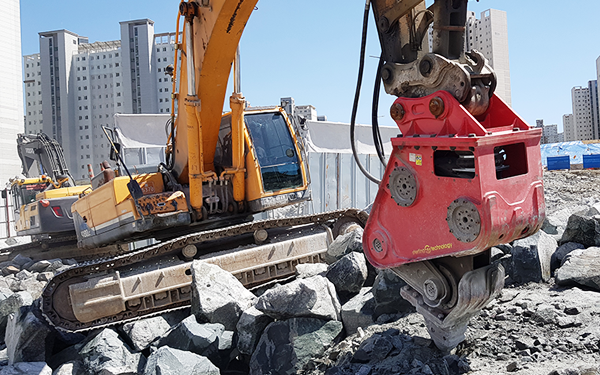
Downtown construction
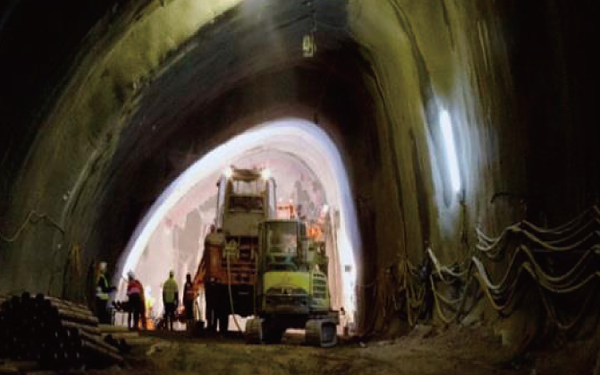
Tunnel Construction
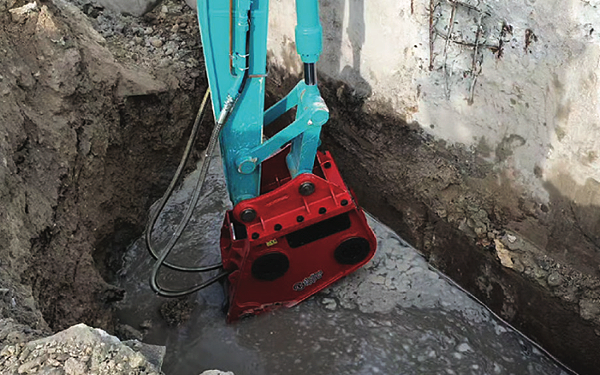
Underwater operation
Specification
Quiet rock breaking technology!Stress & shock free to excavators and operators!
Sterling Ripper offers three options in Tooth type for soft & medium hard-rock, Chisel type for hard-rock for hard-rock, and Compactor type for compacting ground. Single Sterling Ripper body has three optional tools! you can simply change it at site any time depending on rock types and various application!
Tooth type
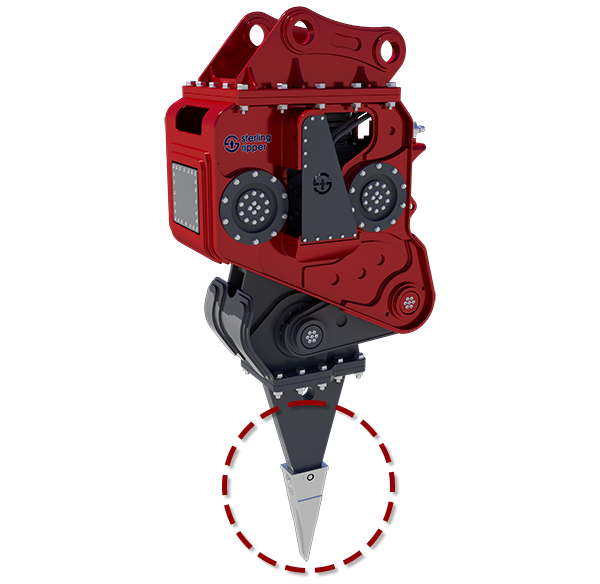
Chisel type
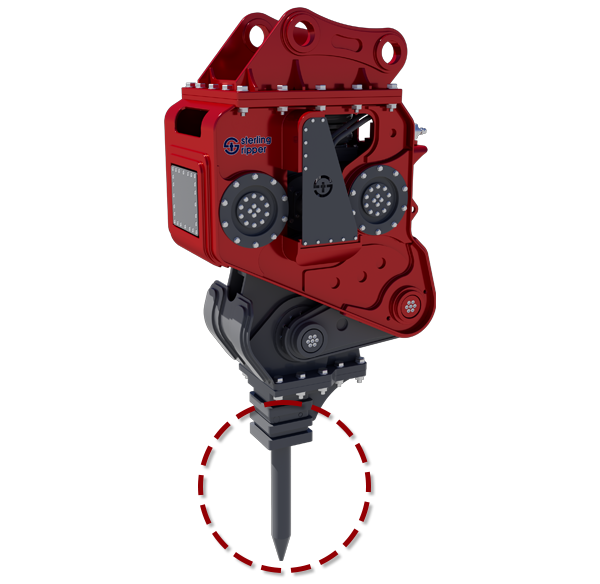
Tip type
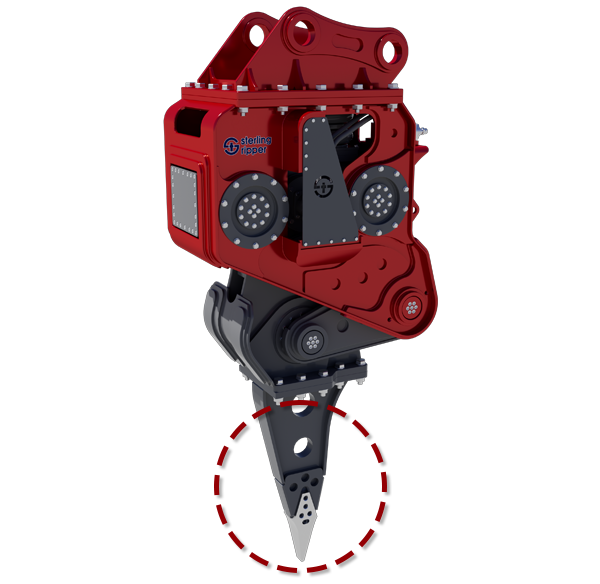
Compactor type
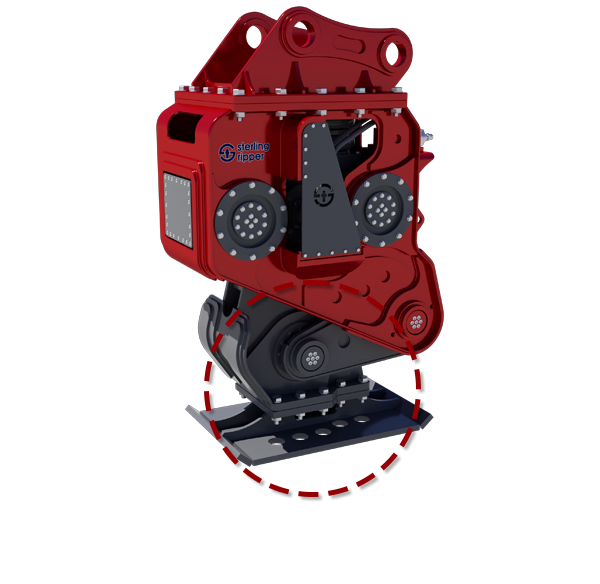
/ UNIQUE CARTILAGE-LINK STRUCTURE AND ROBUST BEARING STRUCTURE OF STERLING RIPPER
- Maximizing productivity and minimizing down time by on-site parts replacement
- Minimizing vibration transmitted to excavator and operator even at hard-rock
- The bigger class of Ripper, the higher productivity
- Rigid and higher durability at hard-rock job site
- Low maintenance
Description | Unit | SR25 | SR30 | SR40 | SR50 | SR80 | |||||
Operating weight* |
Kg | 2,620 | 3,580 | 4,950 | 5,750 | 10,500 | |||||
lb | 5,776 | 7,606 | 9,789 | 12,346 | 23,149 | ||||||
Dimension (AxBxC) |
mm | 855 x 1,361 x 2,983 | 901 x 1,495 x 3,372 | 974 x 1552 x 3585 | 1,130 x 1,713 x 3,920 | 1,490 x 1,640 x 4,304 | |||||
inch | 30.98 x 45.20 x 112.99 | 35.47 x 59.09 x 130.19 | 38.34 x 61.06 x 138.18 | 44.34 x 67.41 x 152.48 | 55.28 x 63.00 x 161.42 | ||||||
Chisel diameter Ø |
mm | 110 | 120 | 130 | 140 | 180 | |||||
inch | 4.33 | 4.72 | 5.12 | 5.51 | 7.09 | ||||||
Relief setting pressure |
Bar | 250 | 250 | 280 | 280 | 300 | |||||
Psi | 3,626 | 3,626 | 4,061 | 4,061 | 4,351 | ||||||
Operating pressure |
Bar | 180-220 | 180-220 | 210-250 | 210-250 | 240-270 | |||||
Psi | 2,610-3,190 | 2,610-3,190 | 3,045-3,626 | 3,045-3,626 | 3,481-3,916 | ||||||
Oil flow |
lpm | 180-230 | 190-250 | 240-300 | 270-330 | 490-580 | |||||
gpm | 47-60 | 50-66 | 63-79 | 71-87 | 129-153 | ||||||
Frequency | bpm | 2,500~3,500 | 2,400~3,200 | 2,200~2,900 | 2,000~2,600 | 1,900~2,400 | |||||
Air spring nitrogen pressure |
Bar | F | R | F | R | F | R | F | R | F | R |
3 | 3.5 | 3 | 3.5 | 3 | 3.5 | 3 | 3.5 | 3 | 3.5 | ||
Psi | F | R | F | R | F | R | F | R | F | R | |
43 | 50 | 43 | 50 | 43 | 50 | 43 | 50 | 43 | 50 | ||
Suitable carrier |
ton | 20~26 | 28~34 | 36~43 | 46~60 | 70~90 | |||||
lb | 44,092 ~ 55,115 | 61,729 ~ 74,957 | 79,366 ~ 94,798 | 101,412 ~ 132,277 | 154,323 ~ 198,416 |
※ Specifications above are subject to change without notice.
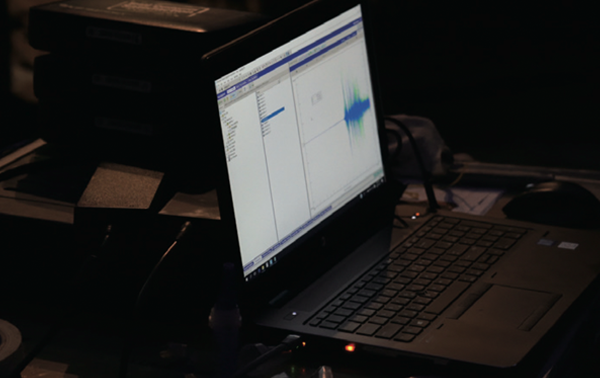
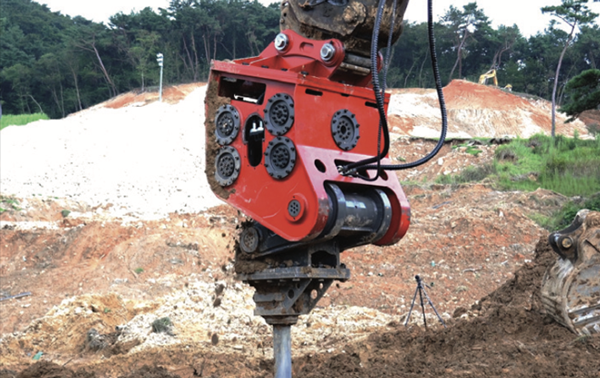
Comparison chart
Available equipment for rock hardness
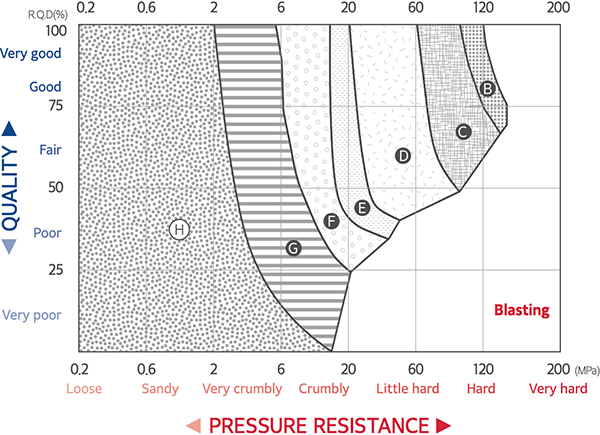
Big class Sterling Ripper can work well at hard rock without problems most vibratory rippers have, thanks to its cutting-edge technology, Unique cartilage-Link
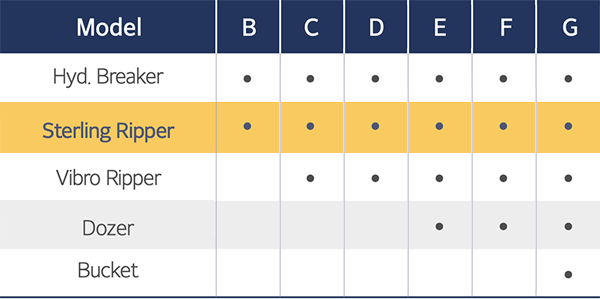
Sterling Ripper VS Hydraulic breaker
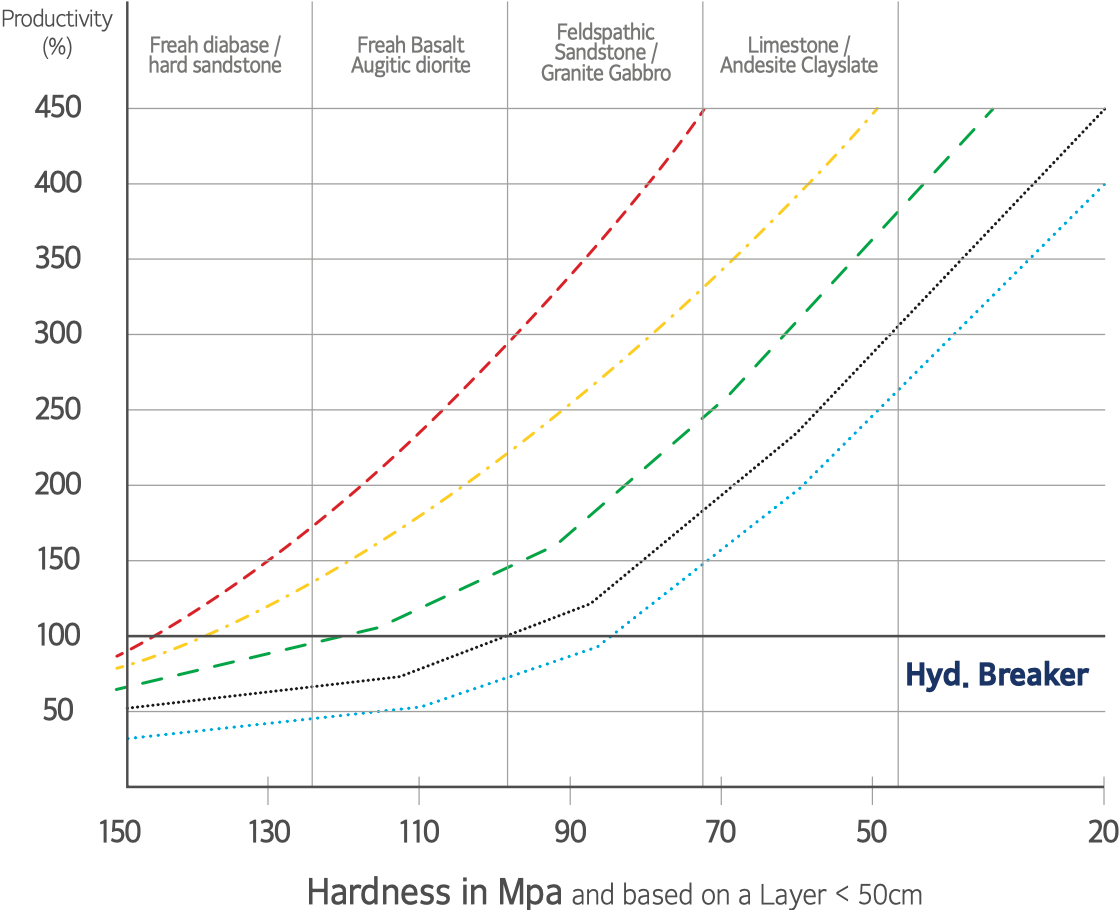
The bigger class of Sterling Ripper, the much higher productivity and hydraulic breaker up to soft medium hard-rock and perform well at hard-rock job site compared to hyd. breaker
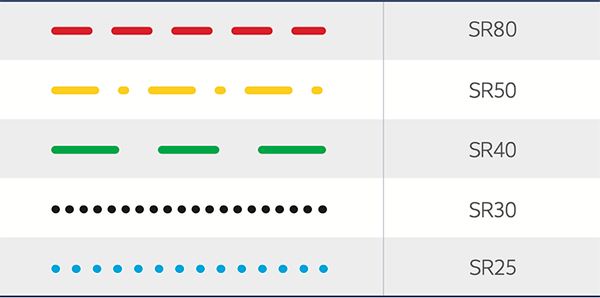
/ STRONG PIONTS OF STERLING RIPPER
Higher productivity than hydraulic breaker
- 2 ~ 8 times better productivity than hyd. breaker depending on type of rocks
More powerful than other vibratory rippers
- Unique structure and design specially bigger and centered eccentric weight
- Sterling Ripper most powerful Ripper in the same class
Selective tool options - Three tools for one Ripper
- Chisel type for hard rock, tooth type for soft & mid hard-rock and Compactor type for compacting ground
- Three optional tools enables Sterling Ripper to offer wider selections of application than competitors at rock breaking job sites
Minimum vibration to excavator and operator at hard-rock
- Unique Cartilage-link of Sterling Ripper allows more powerful striking force but less vibration transmitted to excavator and operator
- Less impact to excavator and less fatigue to operator
Minimum noise
- Sterling Ripper’s Unique Cartilage-link structure technology allows minimum noise at max. 90db and downtown building construction can be done without restrictions
Easy on-site maintenance & low maintenance cost
- Concise structure of components and structure
- Most parts can be replaced at job site
- No need to return it to repair shop
- Less number of parts than competitors enable low maintenance cost
- Maximum productivity can be achieved by reducing down time by on site parts replacement and fast tooth replacement
Under water operation without special devices
- All kinds of work under water can be done without any expensive and complicated preparations
Hyd. Breaker vs Vibratory Ripper
Vibratory Ripper’s advantages compared to Hyd. Breaker
Higher productivity than hydraulic breaker
- Up to 5 times higher productivity than hyd. breaker at less hardness rock formation
- The bigger class of Ripper, the higher productivity
- The less hard rock formation, the higher productivity
- Constant high bpm by vibratory power
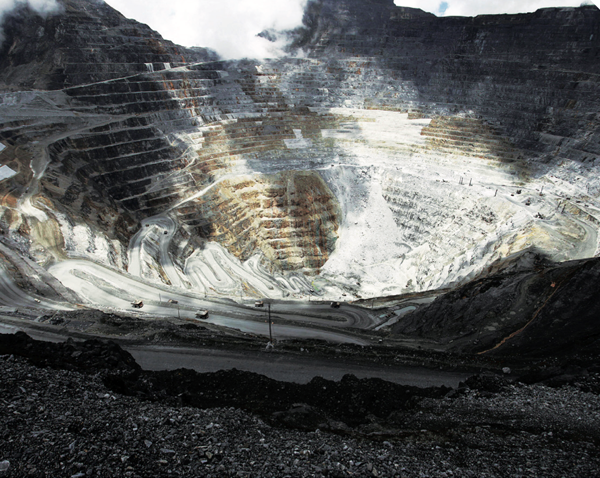
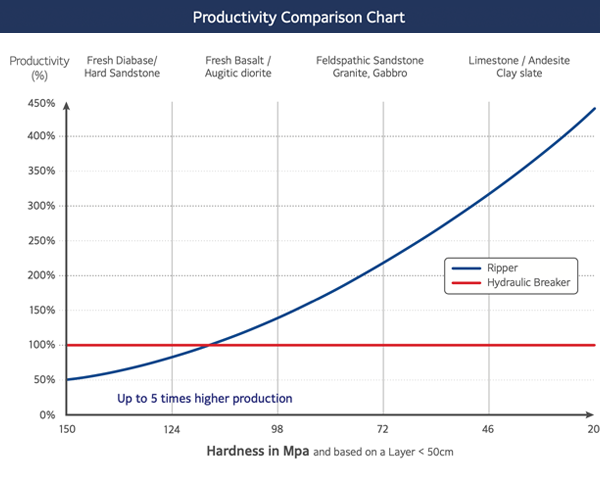
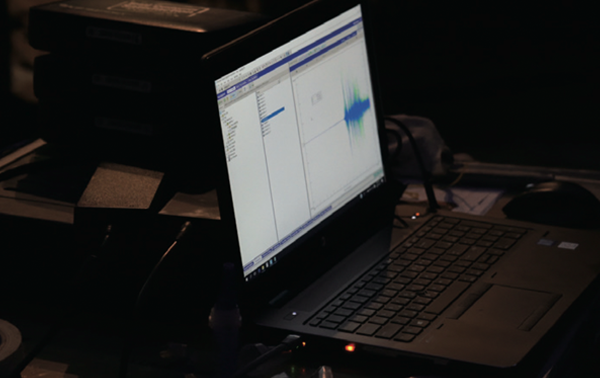
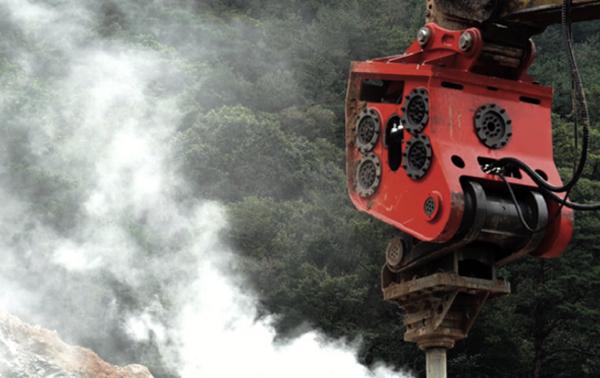
Higher productivity than hydraulic breaker
- 10〜30% less noise than hyd. Breaker
- Less noise(under 90dB) than silent hyd. Breaker
- The less hard rock formation, the less noise
- Minimizing noise at job site allows demolition work in downtown or noise restricted area
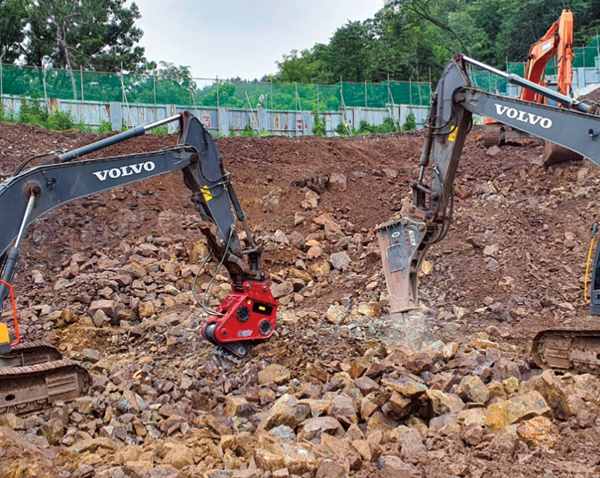
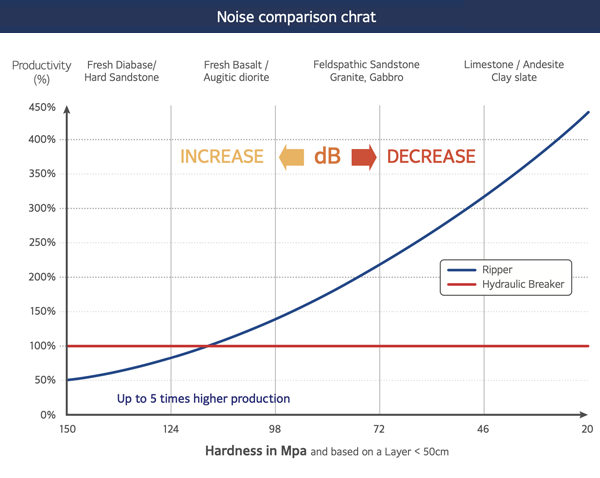
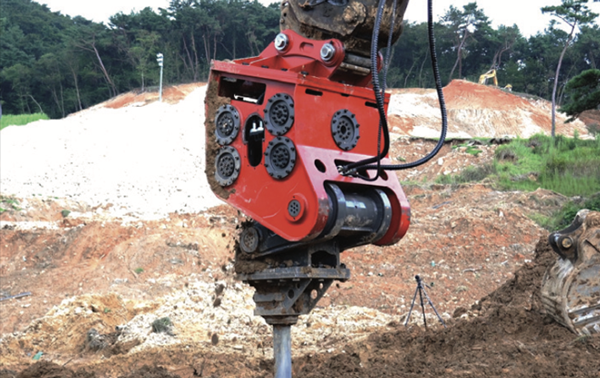
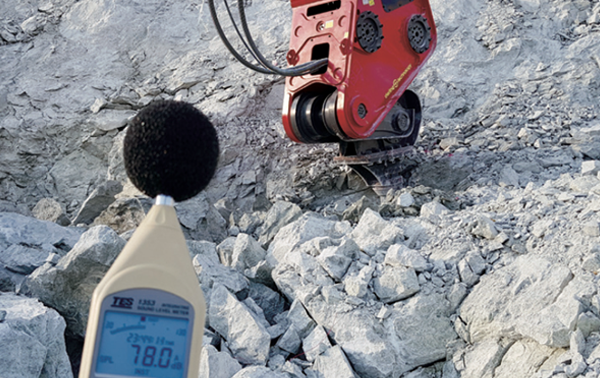
Under water operation without special devices
- All kinds of work under water can be done without any expensive and complicated preparations.
- No need to invest on renting or purchasing air compressors. ex) USD150 〜 450 per day
- No need to spend fuel cost for air compressors. ex) 50liter diesel per hour x 8 hours = USD400 ~ 500 per day
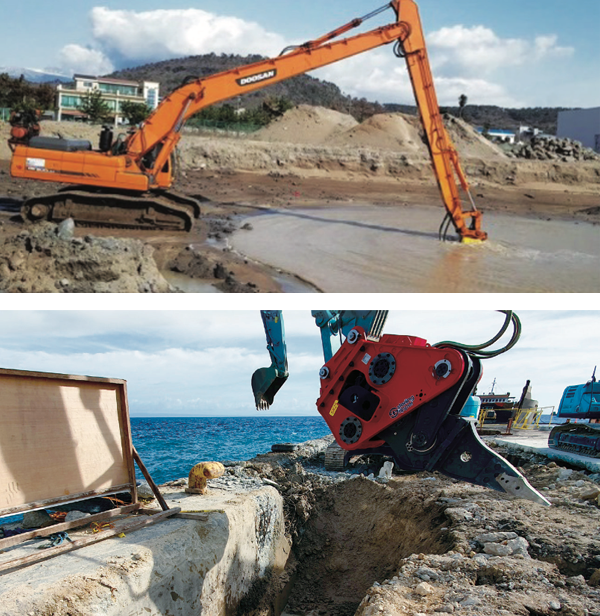
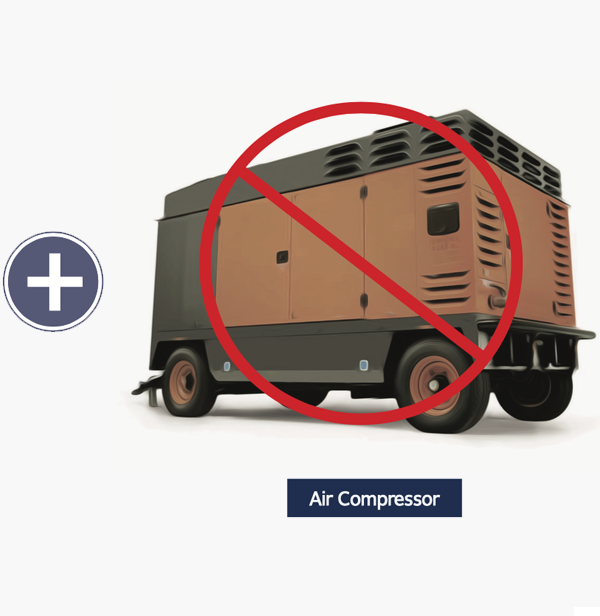
Vibratory Ripper’s draw back compared to Hyd. Breaker
- Lower productivity than hydraulic breaker at hard-rock job sites
- Frequent breakdown in operation at hard-rock job sites due to repulsion energy and constant fatigue to links and bearings of Ripper
- Impact or damage to excavator and increasing operator’s fatigue due to vibration and repulsion transmitted to the excavator and the operator
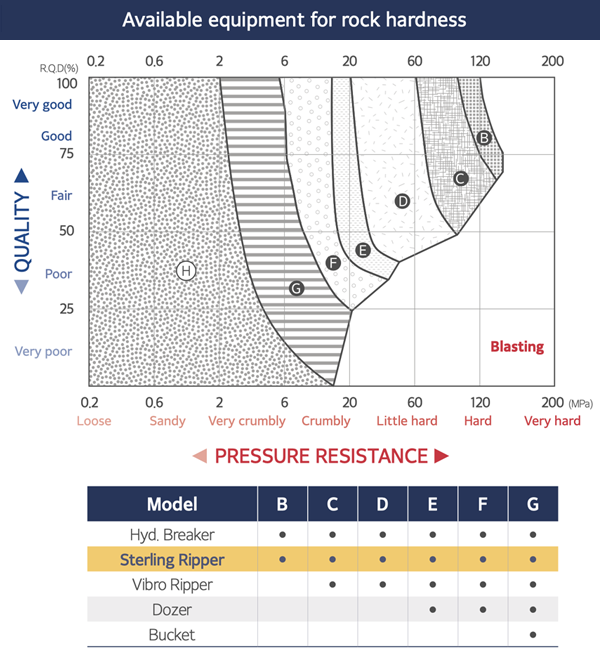
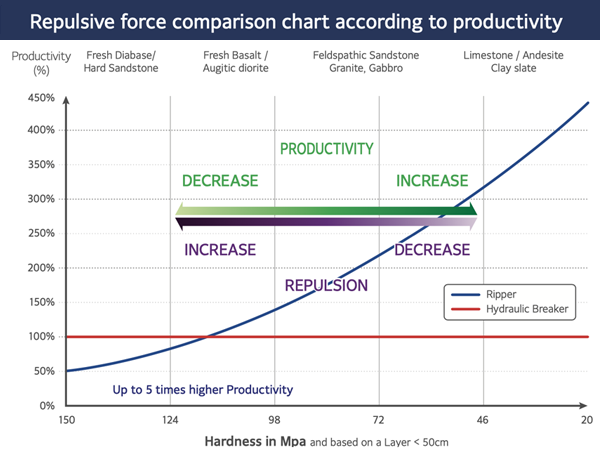
Solution of Sterling Ripper for Vibratory Ripper’s draw back
- Solution for lower productivity than hydraulic breaker at hard-rock job sites
Solution | How to do & Effect |
---|---|
Maximize vibration power |
|
Selective tool options – Two tools for one Ripper |
|
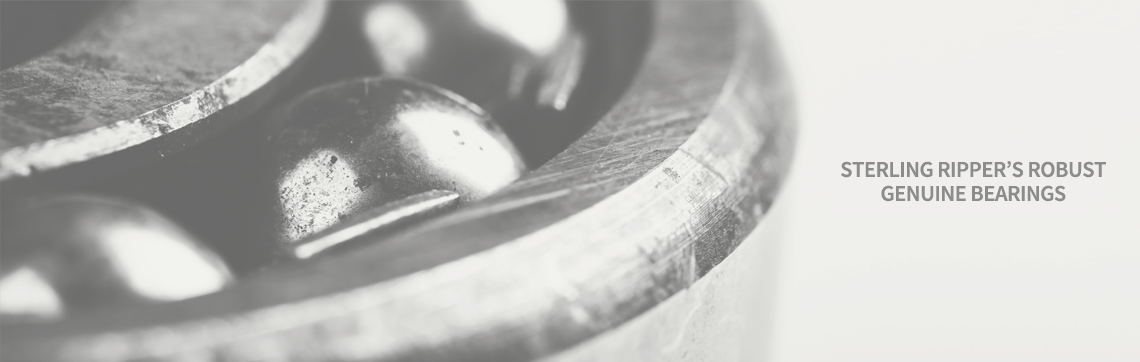
Solution of Sterling Ripper for Vibratory Ripper’s draw back
- Solution for frequent breakdown in operation at hard-rock job sites due to repulsion energy and constant fatigue to links and bearings of Ripper
- Solution for impact or damage to excavator and increasing operator’s fatigue due to vibration and repulsion transmitted to the excavator and the operator
Solution | How to do & Effect |
---|---|
Cartilage-link structure | Use damper cushions with a link instead of bearings with the links to get less repulsion, less noise and no chance of link bearing broken & easy on-site maintenance |
Centered double eccentric weights | Unique design of centered double eccentric weights allow better durability of bearings |
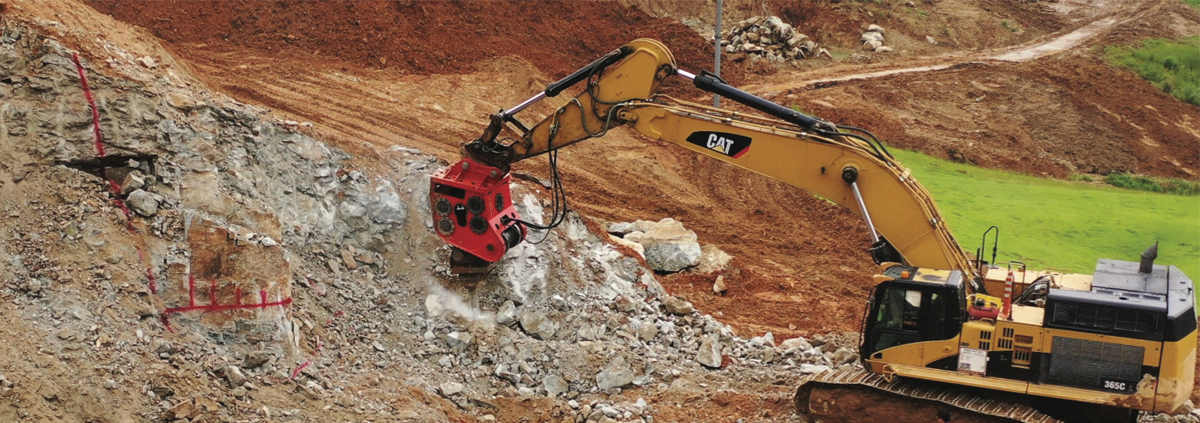
Solution of Sterling Ripper for Vibratory Ripper’s drawback
Solution | How to do & Effect |
---|---|
Cartilage-link structure | Use damper cushions with a link instead of bearings with the link to get less repulsion, less noise and less chance of link bearing broken & easy on-site maintenance |
Conventional Ripper
Main drawback of the link bearing structure
The links and bearings break easily working at hard-rock job sites and Ripper should be sent to maintenance shop to fix it. It takes a lot time and cost which affect total operating cost eventually
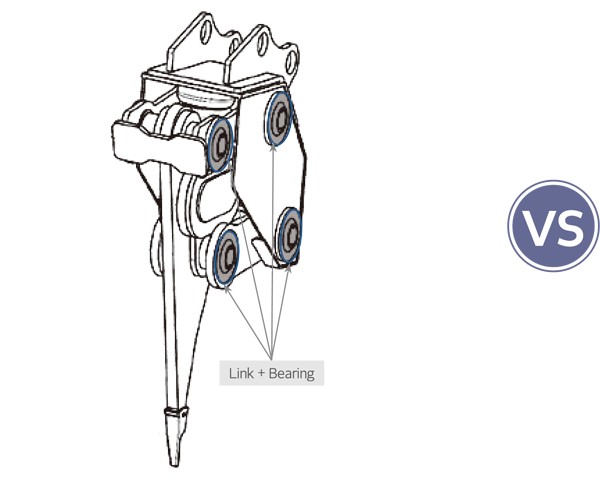
Sterling Ripper
Main advantage of the cartilage link type
Sterling Ripper has adopted damper cushions with a link type instead of link bearing type. It is a very simple process of replacing cushions by simple unscrewing and screwing covers on-site, which allows can save a huge down time and maintenance cost
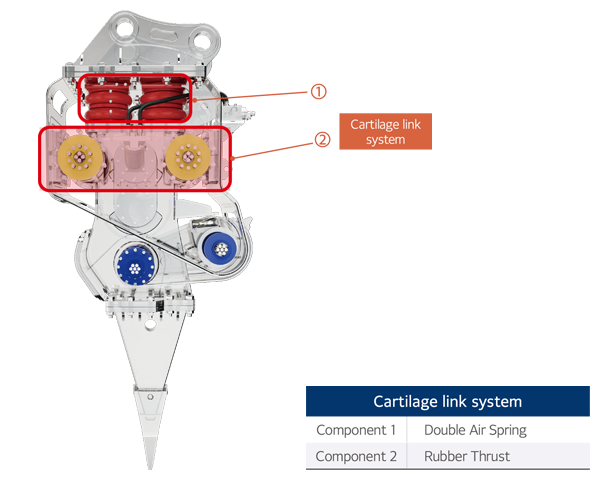
Conventional Ripper’s bearings
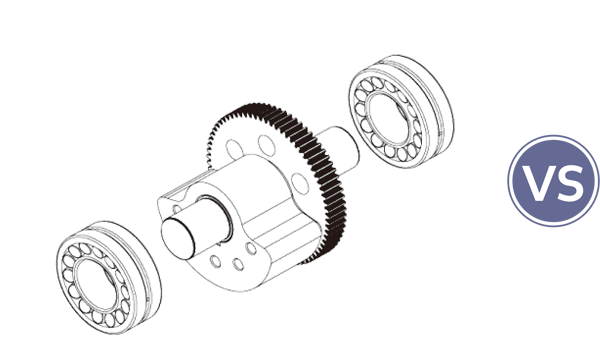
Sterling Ripper’s bearings
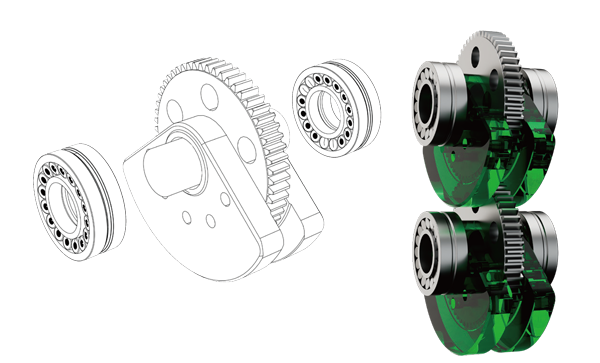
Conventional Ripper’s bearings | Sterling Ripper’s bearings | |
---|---|---|
Advantages | - | High vibratory power at the same size of bearings |
- | At least two times longer life time of bearings | |
- | Higher durability at hard-rock job sites |
Solution of Sterling Ripper for Vibratory Ripper’s drawback
Solution | How to do & Effect |
---|---|
Centered double eccentric weights | Unique design of centered eccentric weights allow better durability of bearings |
Conventional Ripper’s eccentric weights
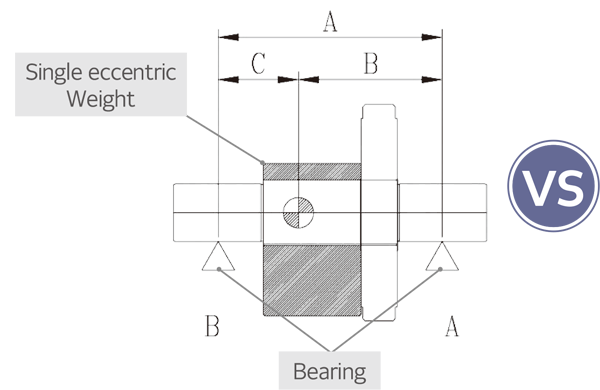
Sterling Ripper’s eccentric weights
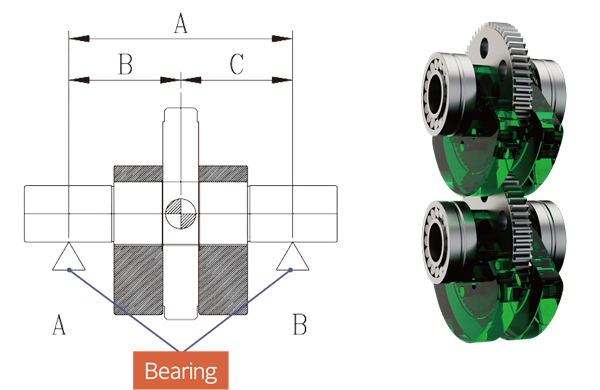
Conventional Ripper’s bearings | Sterling Ripper’s bearings | |
Distance from axis A | A=B+C, B >C | A=B+C, B =C |
Center of gravity | B and C ≠ A/2 | B and C = A/2 |
Weight distribution | “Bearing B” has more weight than "bearing A” | Weight of "A bearing" and “B bearing" is the same |
Effect | Life time of both “A bearing" and “B bearing” is shorten due to imbalance of their weight |
Longer life time of both “A bearing” and “B bearing" |
Solution of Sterling Ripper for Vibratory Ripper’s drawback
Solution for lower productivity than hydraulic breaker at hard-rock job sites - By Chisel type of Sterling Ripper
Sterling Ripper offers three options in Tooth type for soft & medium hard-rock, Chisel type for hard-rock, and Compactor type for compacting ground. You can simply change it at site any time depending on rock types and various application!
Tooth type
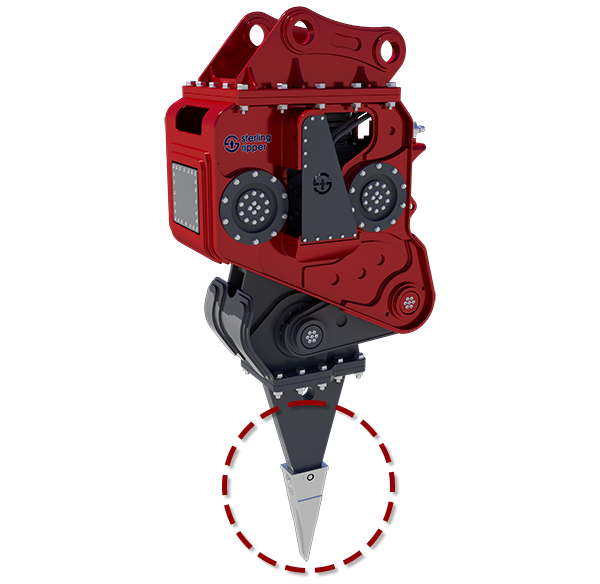
Chisel type
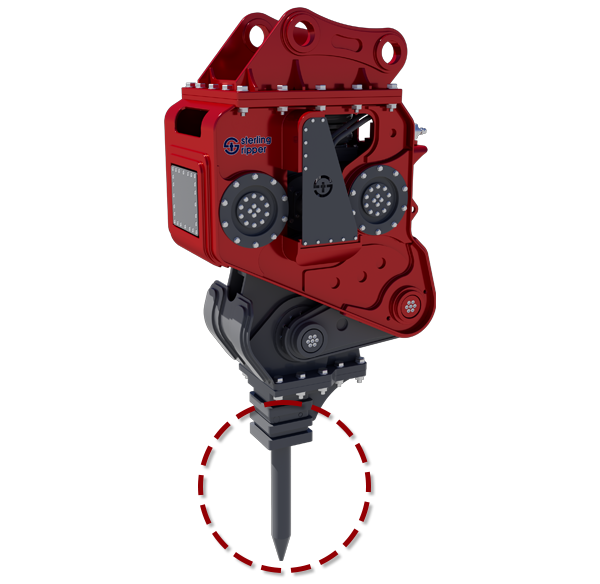
Tip type
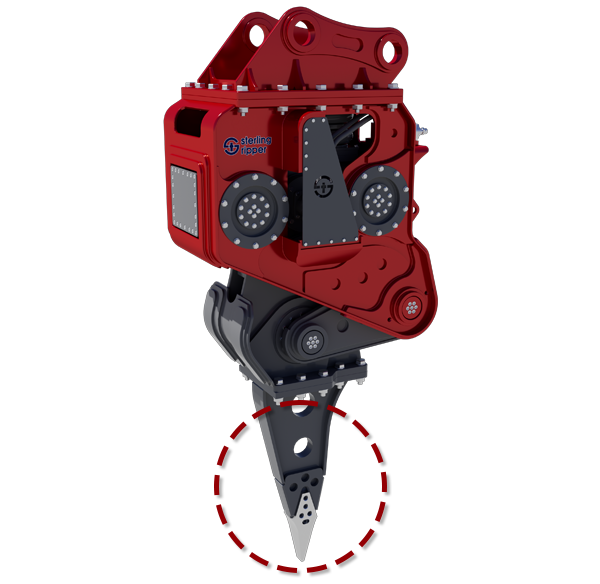
Compactor type
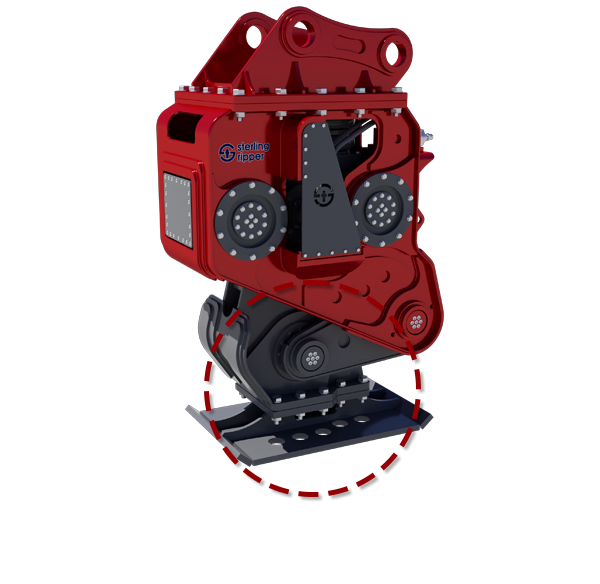
Summary of Sterling Ripper’s selling point
Feature | How to do & Effect |
---|---|
Optimum shape and size of Sterling Ripper’s eccentric weights |
|
Selective tool options - Three tools for one Ripper |
|
Unique Cartilage-link structure of Sterling Ripper |
|
Centered double eccentric weights |
|
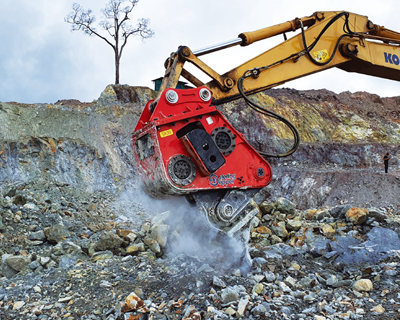
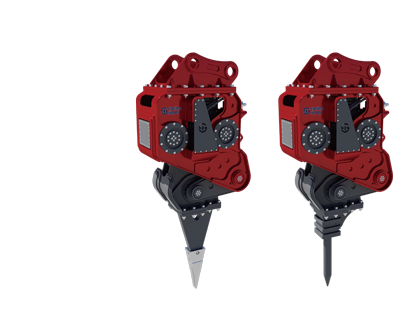
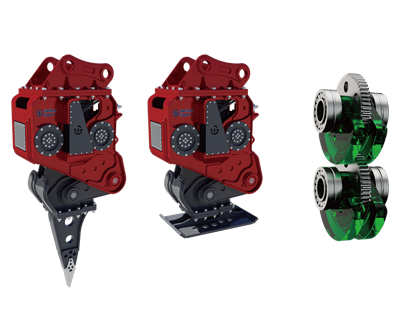
Summary of Sterling Ripper’s selling point
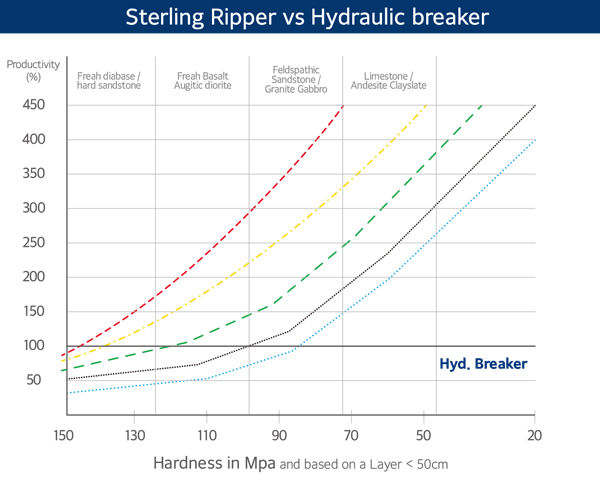
The bigger class of Sterling Ripper, the much higher productivity and hydraulic breaker up to soft medium hard-rock and perform well at hard-rock job site compared to hyd. breaker
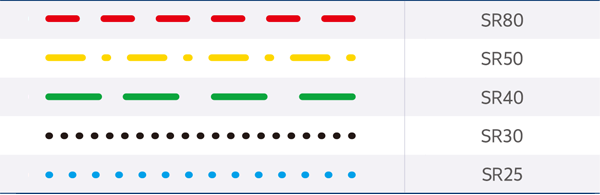
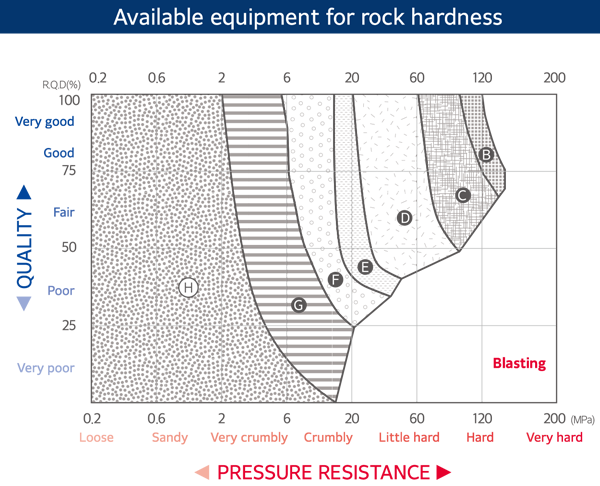
Big class Sterling Rippers can work well at hard-rock without problems most vibratory rippers have, thanks to its cutting-edge technology, Damper+Link structure
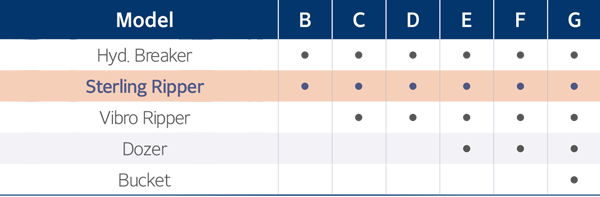